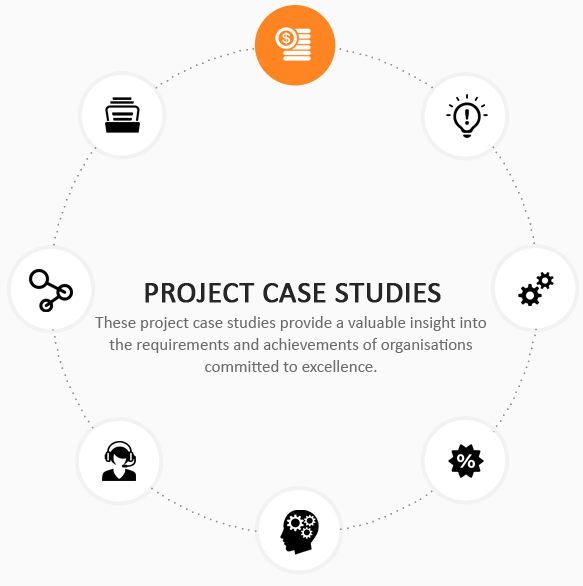
Case Studies
Our collection of case studies draws attention to how organizations are implementing project management practices. These project case studies are provided as an example of how the organisation utilised the University process model to focus on a particular process and undertake.
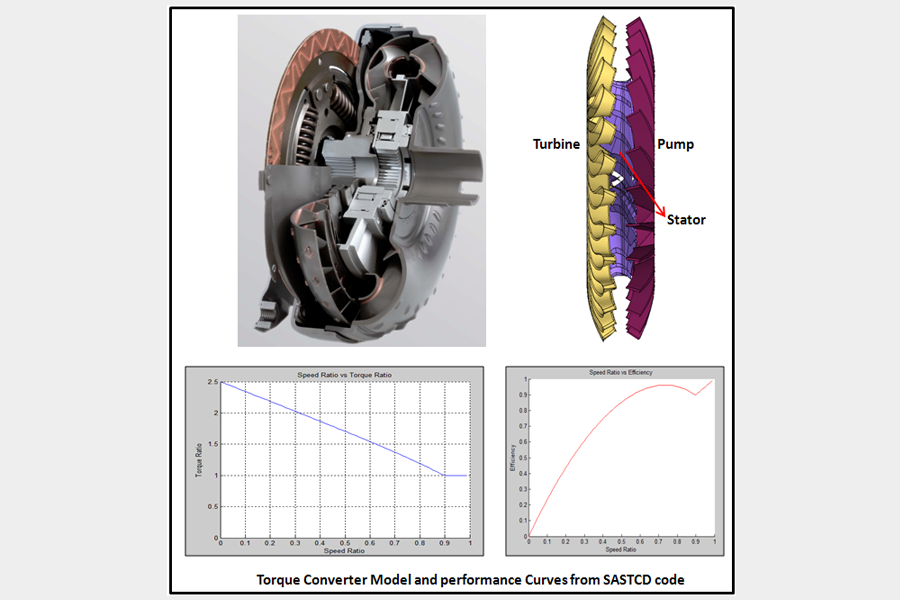
Project-1 Automotive Torque Converter Design Code Development
Torque converter multiplies the torque when there is a substantial difference between engine and transmission rotational speed. Thus, providing an equivalent of a reduced gear. Moreover, the continuous development of transmission for various combat vehicles has led to the need for developing a design procedure for torque converter for various power ratings. In this project, torque converter design methodology is finalized and a standalone program - SASTCD.exe is developed using available open source software. The proposed design code for the development of torque converter facilitated better understanding of the flow field inside the converter to minimize the flow losses leading to improved overall performance of torque converter. This research project has resulted in to development of highly competent code for design of different ranges of torque converter.
Project-2 Design and Development of Semi-Active Suspension system using MR Dampers
This research is aimed at design and development of semi-active suspension system using Magneto Rheological (MR) dampers and it’s technology transfer. Now a days, the MR damper is one of the most promising new devices for heavy machinery and structural vibration reduction. MR damper meets the demands of many applications efficiently, because of its large force capacity, robustness, low power requirements, mechanical simplicity and high dynamic range. In recent years, MR dampers have received significant attention since they offer the adaptability of active control devices without requiring the coupled large power sources. MR damper potentially offers highly reliable operation as it can act as a passive damper during power failure mode. Further, MR damper is designed based on parameters like shear gap and size of the MR valve, MR fluid selection, magnetic circuit design, electromagnetic analysis, analytical damping force estimation, material selection and feasible manufacturing techniques. The designed damper has been tested using servo hydraulic machines and damping characteristics have been recorded. The research of this project has led to the development and transfer of innovative MR technologies for semi-active suspension design.
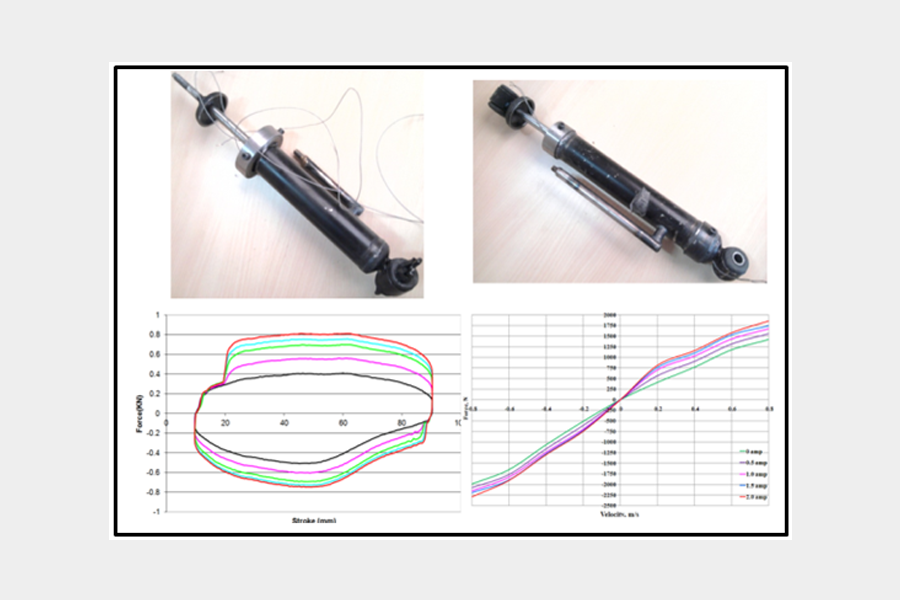
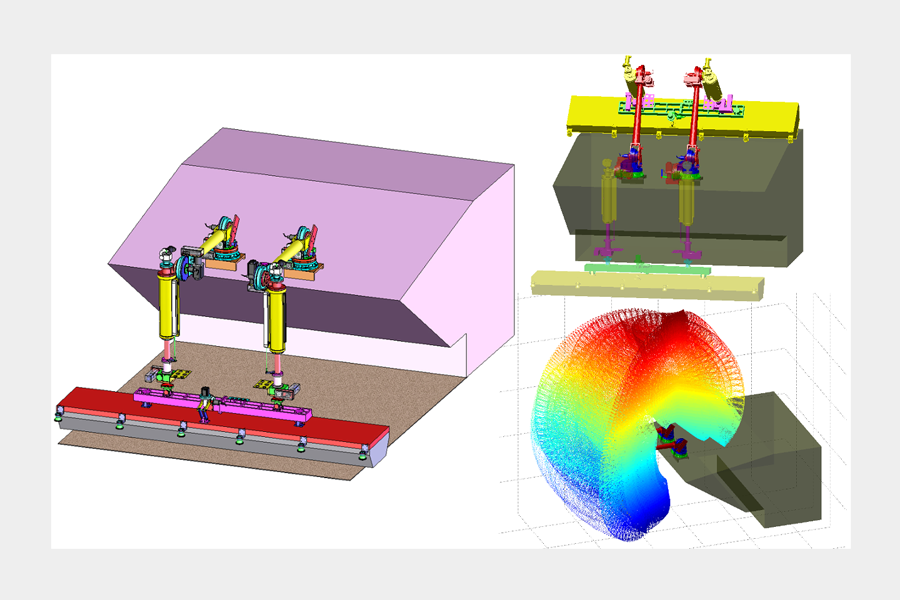
Project-3 Kinematic and Dynamic Analysis with Trajectory Planning and FEA of the Arm Assembly of Mobile Manipulator mounted on an Armed Tank
This research is aimed at Kinematic and Dynamic Analysis with Trajectory Planning and FEA of the Arm Assembly of Mobile Manipulator mounted on an Armed Tank. The mine detection manipulator system mounted on an reconnaissance tank comprises of two serial manipulators working together as a dual-arm cooperative manipulator and carries the GPR, vapor detection and LIDAR sensors, the former two sensors detects for the presence of mines buried underneath the ground surface and the latter measures the distance from ground.
The operation of the mine detection manipulator involves detection of mines while the tank is in the motion by swinging the sensor assembly linearly sideways to increase its coverage area while also maintaining the optimal ground clearance by dynamically adapting to the unpredictable terrain. During off duty the manipulator assembly is fold and rest on the tank for its safety and deployed to its ready pose when needed.
The operation of the mine detection manipulator involves detection of mines while the tank is in the motion by swinging the sensor assembly linearly sideways to increase its coverage area while also maintaining the optimal ground clearance by dynamically adapting to the unpredictable terrain. During off duty the manipulator assembly is fold and rest on the tank for its safety and deployed to its ready pose when needed.
Project-4: CFD Analysis for Cooling Systems of 1500HP Power Pack
This research is aimed at computationally estimation of heat balance, air flow distribution and pressure loss across radiators, louvers, cooling air ducts in the given configuration and to Optimize the cooling air duct geometry for the given two set of configuration.
The cooling system forms an intrinsic part of an engine. It performs multitude of functions such as removing excess heat from the engine, maintaining efficient temperature and allowing engine to perform its task within a short span of time. Ideally, cooling system keeps the engine running at an optimum temperature whatever the operating conditions are. Vehicle Cooling System consists of components installed in vehicles for removing heat from all the moving parts so that they can work suitably without melting, seizing and overheating. This project proposes a three-dimensional flow simulation to investigate the of pressure loss (∆P) across radiators, louvers, cooling air duct and to Optimize the cooling air duct geometry for the given set of configuration.
The cooling system forms an intrinsic part of an engine. It performs multitude of functions such as removing excess heat from the engine, maintaining efficient temperature and allowing engine to perform its task within a short span of time. Ideally, cooling system keeps the engine running at an optimum temperature whatever the operating conditions are. Vehicle Cooling System consists of components installed in vehicles for removing heat from all the moving parts so that they can work suitably without melting, seizing and overheating. This project proposes a three-dimensional flow simulation to investigate the of pressure loss (∆P) across radiators, louvers, cooling air duct and to Optimize the cooling air duct geometry for the given set of configuration.
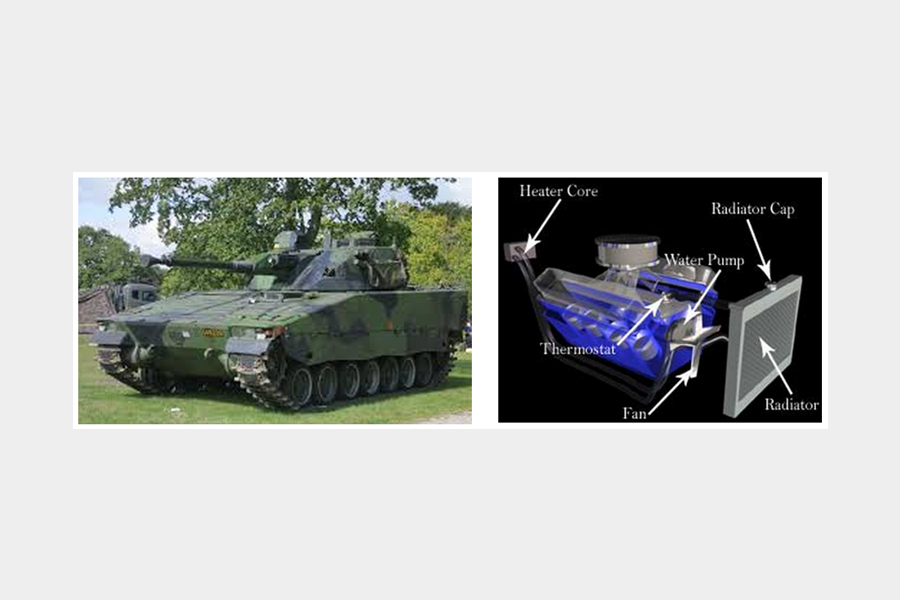
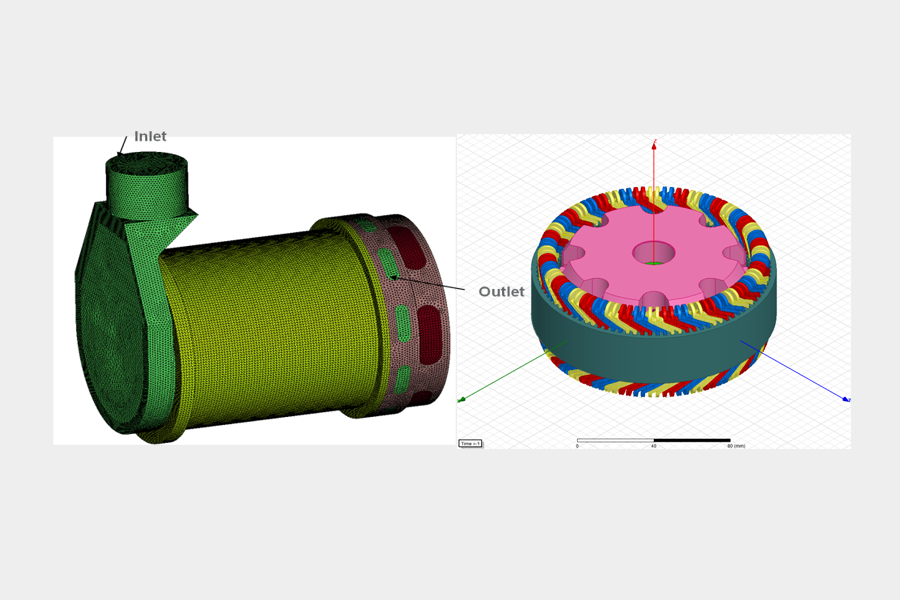
Project-5: Design analysis of BLDC Generator:
In this work, optimization of a brushless direct current (BLDC) generator design was undertaken by carrying out an electromagnetic and computational fluid dynamic study. The studies were carried out for different loading-overloading conditions and angular speeds, keeping in consideration the required electrical and thermal parameters, firstly for the initial design and then for optimized designs. In the initial phase, transient electromagnetic simulations were done using Ansys Maxwell to estimate power output, flux densities, heat losses et al. In the next phase, steady state conjugate heat transfer simulations using frozen rotor method for rotating domains were carried out in Ansys CFX using the heat loss values obtained from electromagnetic study in the first phase. The results from conjugate heat transfer were obtained in the form of temperature and flow parameters. After a thorough study and comparison of the results for different designs, obtained in the two phases, it was seen one of the optimized designs showed better electromagnetic, thermal and flow parameters as compared to the initial design and satisfied all the optimum electrical and thermal parameters.
Project-6 Structural Evaluation of Airborne Winch Drum & Assembly
Winch system is a multidisciplinary system involving hydraulic controls, electric drives, gearbox, sensors, structures, mechanisms and electronic circuitry. Verification of the structural characteristics and dimensional modification of the structural elements to ensure the required strength and stability condition of Airborne Winch Systems requires finite element analysis of the system. Static analysis was performed to determine deformations and stresses under operation and structural condition. Modal Analysis was conducted to determine frequencies and mode shapes under operation and structural condition. Also, to determine the response of the system, the model has been subjected to shock loads in all three directions. Finite element model was created using HyperMesh. Finite Element analysis and post-processing the results was carried out using ANSYS.
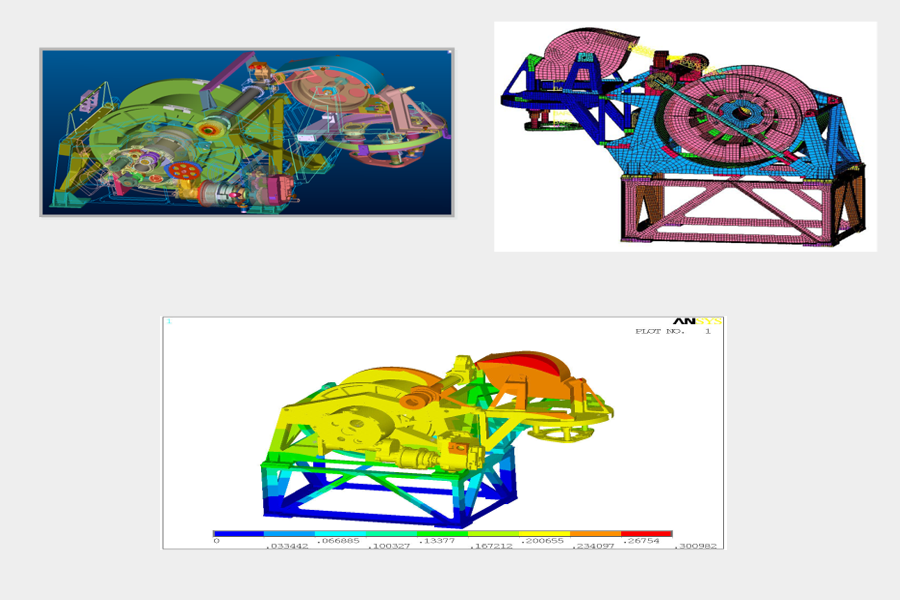
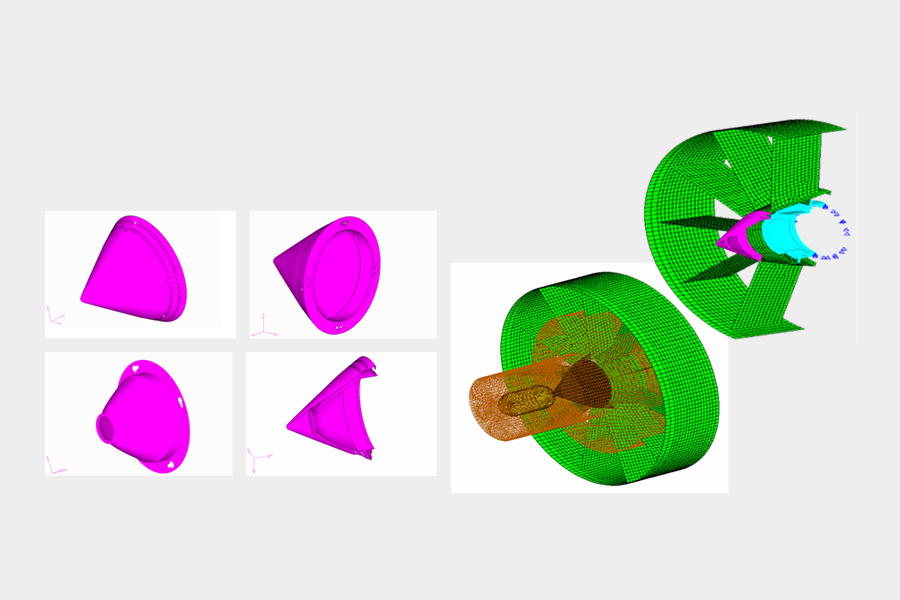
Project-7 Bird Hit Analysis of Bullet Nose of Aero-Engine
All aircraft components are vulnerable to bird impact and hence, it becomes necessary for the components to be designed against bird impact. In spite of the experimental technique being a foolproof method of testing a component after preliminary design, the huge cost and time involved renders the technique, impractical. Hence it is required to develop a reliable methodology using finite element analysis to simulate the bird hit event. Bird impact on aircraft is a soft body impact, which is very much different from elastic impact. Accurate numerical solution demands the proper selection of the parameters such as the shape of bird projectile, density of a bird material and length to diameter ratio, before simulating the bird impact analysis. This project investigates the influence of impact angle and impact velocity in the structural response. Two different size of bird has been simulated as hemispherical ended projectile with gelatine as material. Simulation has been performed in LS-Dyna.
Project-8 Development of Design Methodology, Fabrication and Testing of MR Mounts
The mixed mode MR mount is designed with proper utilization of dimensional parameters and the high performing damping characteristics. The materials and dimensions are finalized by carrying out structural and electromagnetic analysis. The suitable rubber to withstand static load is selected based on the usability, load and static deflection. Individual components are fabricated and assembled ensuring leak proof, fail safe and testing platform alignment. The behavior of the MR mounts with control elements is compared with that of the passive mounts. The tests for each MR mount with electronic controllers is conducted at BISS, CQAE and CPRI as per MIL standards (167 and M 17185 A). Characterization of the MR mount has been carried out for different load capacities. This project has led to the development and transfer of innovative MR technologies for damper design.
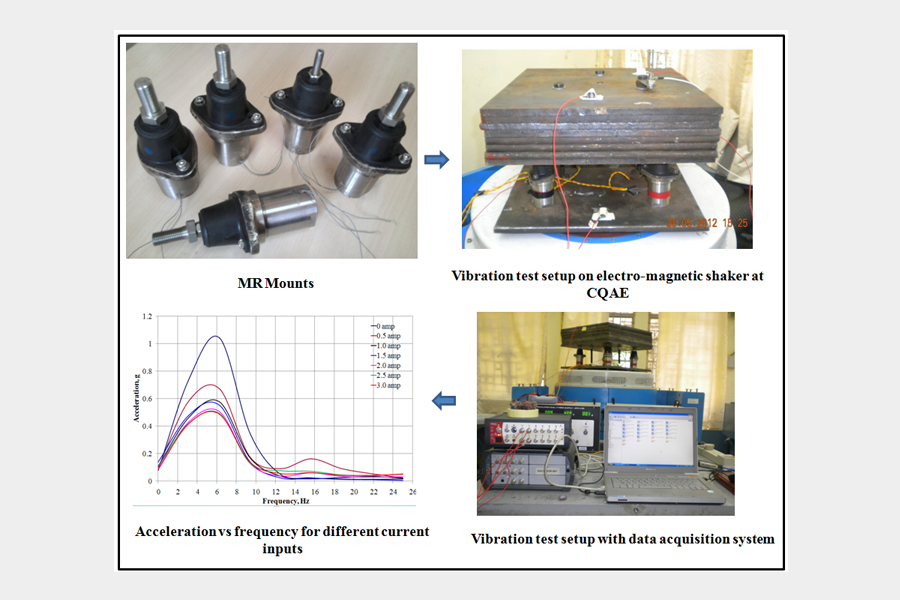
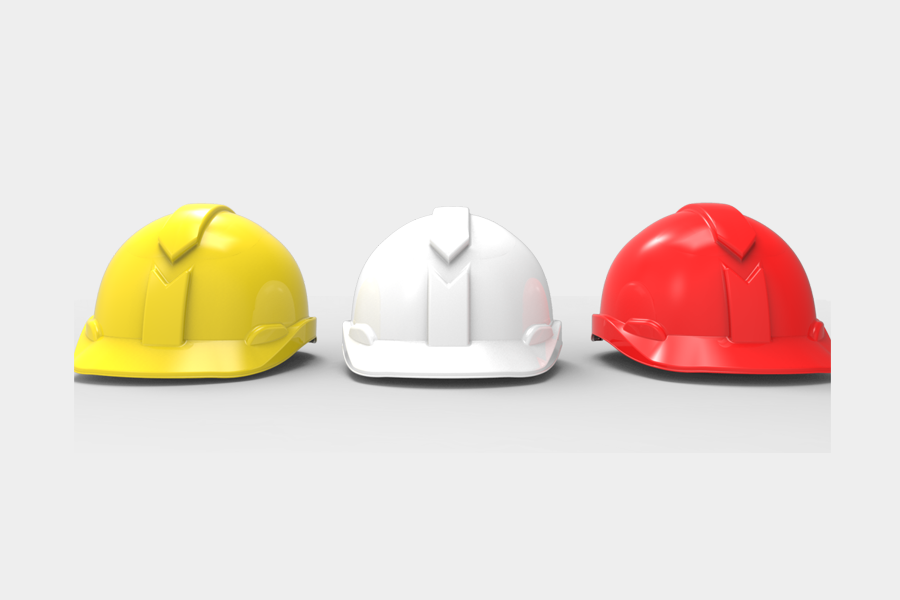
Project-9 Design of Safety Helmets
A safety helmet is a type of helmet predominantly used in workplace environments, such as construction sites/mining industries, to protect the head from injury by falling objects, impact with other objects, debris, bad weather and electric shock. Helmet inner construction consist of suspension that spreads the helmet's weight over the top of the head. It also provides a space between the helmet's shell and the wearer's head so that if an object strikes the shell, the impact is less likely to be transmitted directly to the skull. Sometimes the helmet shell has a mid-line reinforcement ridge, which strengthens it against impact. At RUAS-Techno Centre Engineering, a safety helmet for one of the private industry is designed by the consideration of safety, aesthetics and sturdy look with cost effectiveness.
Latest trends and need for safety helmets was gathered from market survey. More than 5 concepts are generated and finally the above shown concept was finalized. Impact and penetration test were simulated as per as BIS standard using FEA tool-LS-Dyna and designed helmet shows satisfactory results for standard test procedure. Materials(HDPE+EVA+Talc powder) for safety helmet construction was also suggested by keeping cost effectiveness criteria.
Latest trends and need for safety helmets was gathered from market survey. More than 5 concepts are generated and finally the above shown concept was finalized. Impact and penetration test were simulated as per as BIS standard using FEA tool-LS-Dyna and designed helmet shows satisfactory results for standard test procedure. Materials(HDPE+EVA+Talc powder) for safety helmet construction was also suggested by keeping cost effectiveness criteria.
Project-10 Home Automation Products
Home Automation Product offers all of the smart home technologies like controlling of light (Intensity control), home security and customized scene settings. A detailed case study has been carried out on existing and new home automation technologies available in the market and selection of suitable protocols has been done for home automation as per the requirements.
Different products coming under Home Automation Products are Touch dimmer, infrared remote, Floater Pad and Touch user interface. Different lights in different regions can be controlled using these products where each product has its own advantages. Different scene settings can be customized by the user according to his usage and mood (Evening scene, Movie scene and Night scene...etc)
Different products coming under Home Automation Products are Touch dimmer, infrared remote, Floater Pad and Touch user interface. Different lights in different regions can be controlled using these products where each product has its own advantages. Different scene settings can be customized by the user according to his usage and mood (Evening scene, Movie scene and Night scene...etc)
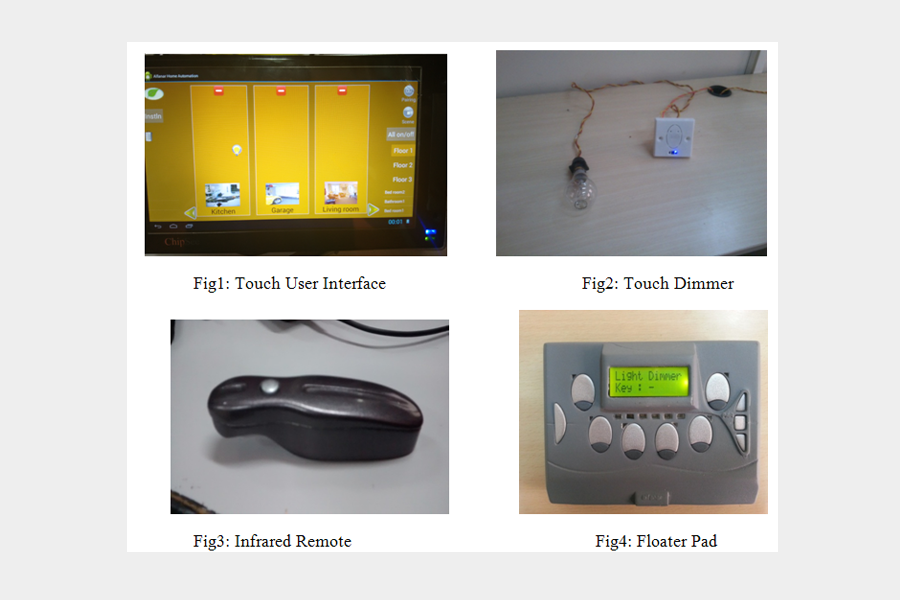
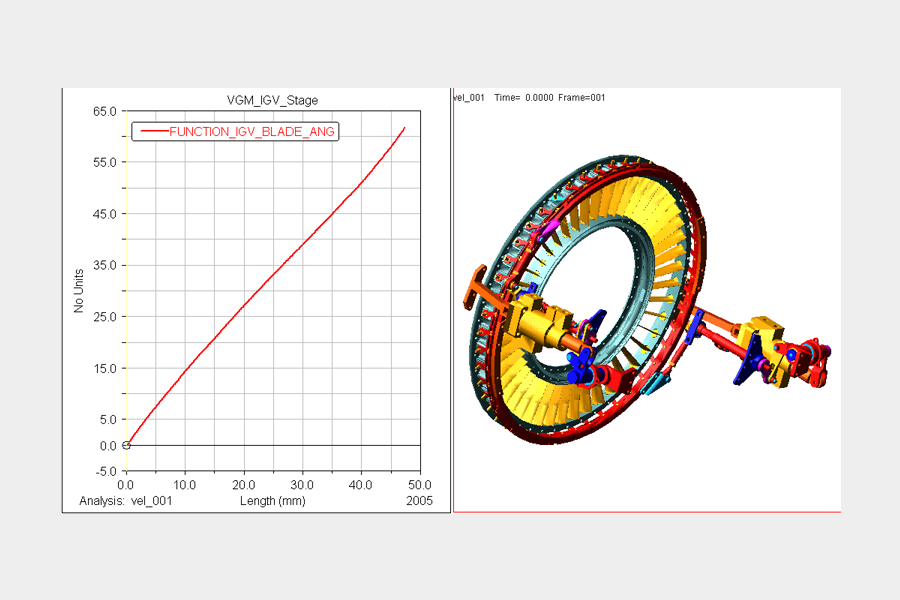
Project-11: Kinematic and Dynamic Analysis of Guide Vane Mechanism
The Guide Vane Mechanism is used to control the airflow through the aircraft engine. The mechanism consists of an actuation system and three individual stages. The actuation system consists of two actuators (master and slave). An individual stage of GM system consists of vanes, which are distributed radially around the circumference of the engine, which each of vane connected to an actuating lever. All of the actuating levers are connected to the actuating ring through spherical bearings. The actuating ring rotates about the axis of the engine by connectors from the actuation systems. As the actuating ring is rotated, all of the vanes should rotate an equal amount.
The Guide Vane Mechanism is subjected to various loading conditions. Hence it is very important to evaluate the structure of the GM through various analyses. Kinematic analysis, Link length optimization, Dynamic analysis & Finite element Analysis of Guide Vane Mechanism for the given different input condition was carried out.
The Guide Vane Mechanism is subjected to various loading conditions. Hence it is very important to evaluate the structure of the GM through various analyses. Kinematic analysis, Link length optimization, Dynamic analysis & Finite element Analysis of Guide Vane Mechanism for the given different input condition was carried out.
Project 12: Kinematic and Dynamic Analysis of CD Nozzle
The exhaust system of the aero Engine has a convergent-divergent nozzle which was designed and developed by DRDO with assistance from academia . This type of nozzle is capable of producing thrust only in the axial direction and is not designed to tilt the thrust line away from the engine axis. In case of military gas turbine engine development there is a constant endeavor to improve and upgrade integrated performance of engine and aircraft. The requirement of developing CD technology is projects as a part of DRDO’s Long Term Technology Perspective Plan. DRDO is pursuing design and develop a technology demonstrator of a Mechanical Multi-axis CD Nozzle. Vectoring will be achieved by deflection of divergent flaps only and there will be independent exit area control. The knowledge and experience gained in this project will be useful for designing the thrust vectoring nozzle for indigenously developed aircraft engines.
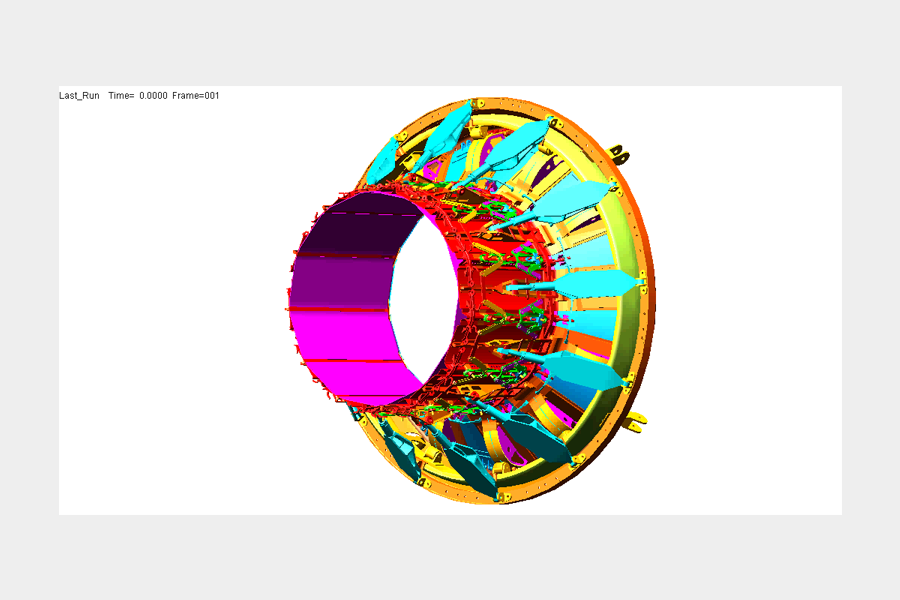
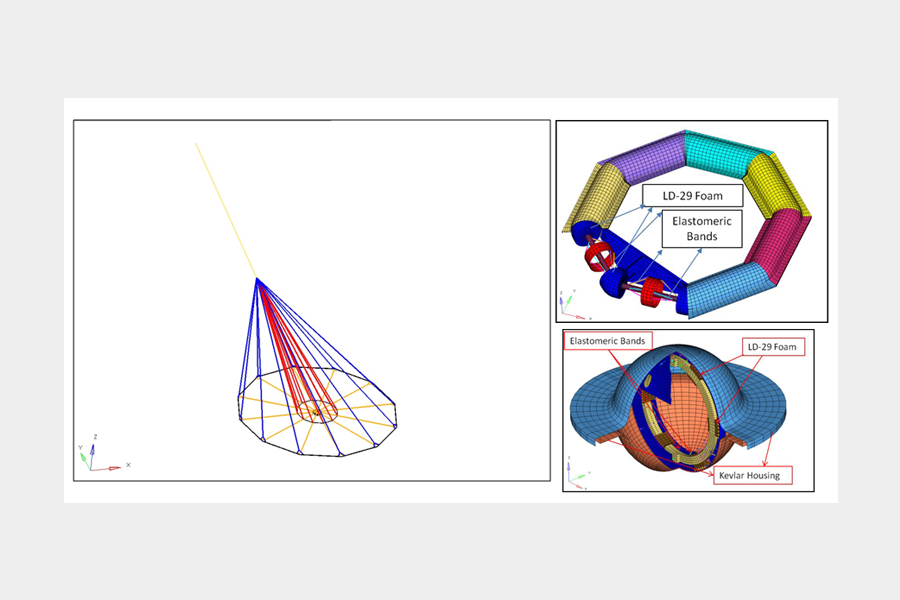
Project-13: Design & FE Analysis of Helicopter Borne Under-Slung System
The helicopter borne under-slung assembly is composed of a system of concentric transmitter, bucking and receiver coils in tubular housings all held in place by a system of suspension and radial ropes. In flight, the entire assembly is in equilibrium under aerodynamic and gravitational loads. The assembly thus is likely prone to aero-elastic instabilities such as buffeting.
Dynamic aero-elastic characteristics such as flutter are known to depend on the underlying modal characteristics in coupled flow. For vortex-shedding phenomena however, in-vacuo modal characteristics typically govern the associated critical flow speeds. Accordingly the present study is aimed at obtaining modal solutions of the under-slung assembly in-vacuo.
The FE solutions have been satisfactorily correlated with hand estimates of modal frequencies wherever feasible. Both FE solutions and hand estimates have been obtained to fulfill wind tunnel test requirements.
Dynamic aero-elastic characteristics such as flutter are known to depend on the underlying modal characteristics in coupled flow. For vortex-shedding phenomena however, in-vacuo modal characteristics typically govern the associated critical flow speeds. Accordingly the present study is aimed at obtaining modal solutions of the under-slung assembly in-vacuo.
The FE solutions have been satisfactorily correlated with hand estimates of modal frequencies wherever feasible. Both FE solutions and hand estimates have been obtained to fulfill wind tunnel test requirements.